Rigid/Soft PVC Sheets / imitation marble board Extrusion Line
designed Rigid PVC sheets extrusion line adopts mixer, conical twin screw extruder, T die head, three roller calendars and downstream parts, including cooling frame and edges trimming, decoration film coating unit, corona unit as optional, haul off machine and also the transverse cutter and conveying table.
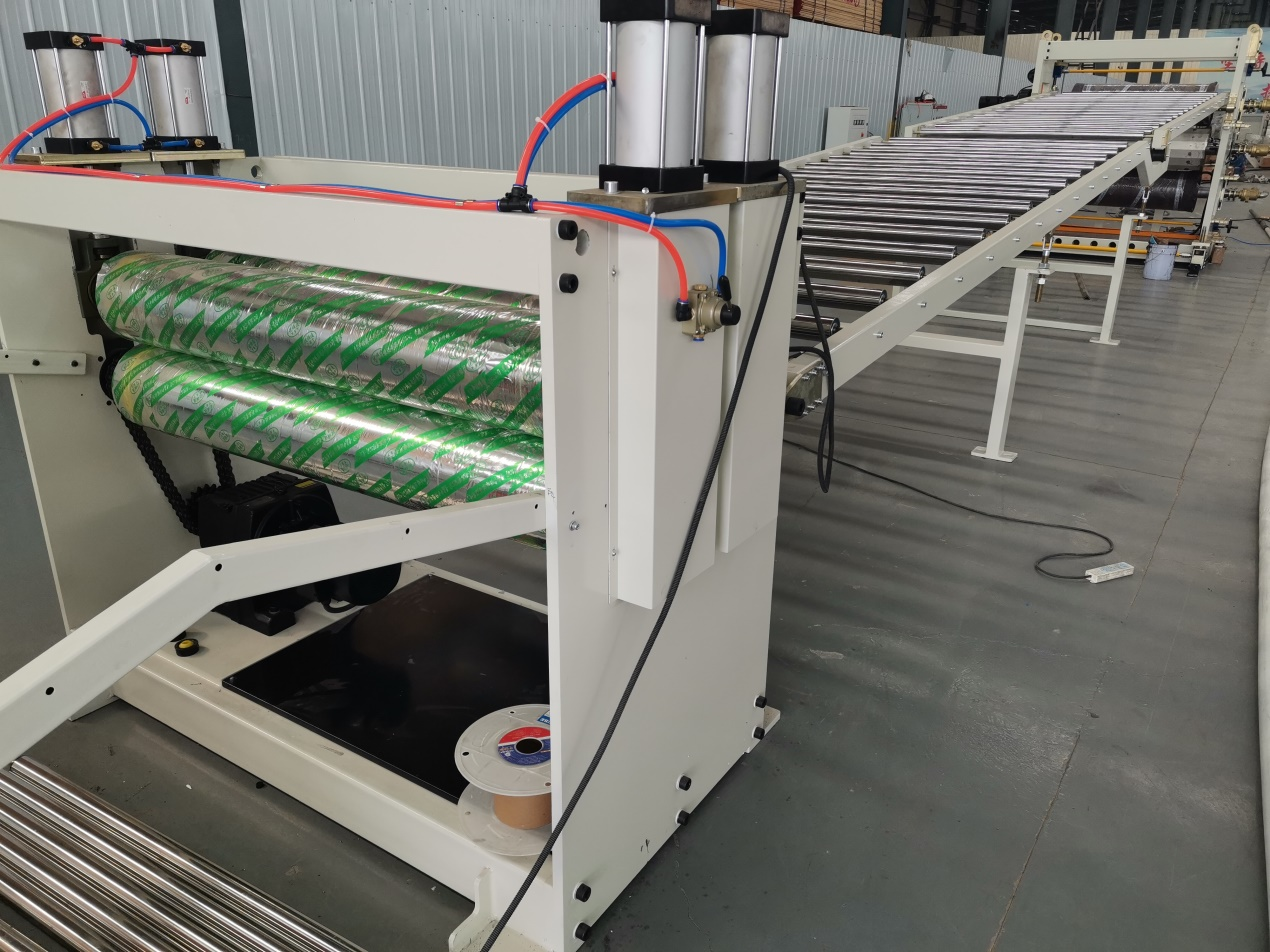
The extruded rigid PVC opaque sheets are easy to form, high tension, various colors, fireproof, high quality, low cost, applied to different kinds of fields, such as sandwich panel in construction field, furniture edge banding and skinning, high standard printing, thermoforming packing, advertising, interior decoration etc.
PVC transparent soft sheet is product instead of the traditional door curtain. It is soft, clear, insulation, safe, environmental protection, acid resistance, no peculiar smell, easy to clean, and etc, also can be used in cold and heat insulation, save energy,windproof, keep humidity, anti-corruption, fire proof, anti static. ultraviolet radiation proof, sound proof, table pad, daylighting, Industrial damping, safety warning ,protect surface, these application used in refrigeration, foodstuff, printing, weaving, electrics, instrument, medicine, storage. It has good effect on insulation for electricity, and harmful light.
The imitation marble sheets, also called “calcium powder high-filled PVC composite material”, “stone plastic material”, “high calcium material”, “imitation marble material” etc. This imitation marble sheets are featured with frienly environmentally, ultra-light and ultra-thin, super wear-resistance,high impact resistance, fire retardant, moisture and water proof, sound absorption and noise prevention, easy clean, widely used in various places, such as indoor decoration, hospitals, schools, office buildings, factories, public places, supermarkets, commerce, stadiums and other places.
Extruder model
Item | SJSZ 65/132 | SJSZ 80/156 | SJSZ 92/188 |
Screw Diameters(mm) | 65mm/132mm | 80mm/156mm | 92mm/188mm |
L/D Ratio | 22:1/25:1 | 22:1/25:1 | 22:1/25:1 |
Output(Kg/h) | 160-200 | 250-350 | 400-500 |
Main Driving Power(kw) | 37 | 55 | 110 |
Heating Powder(Kw) | 4 zones, 20Kw | 5 zones, 38Kw | 6 zones, 54Kw |
Details
01 Conical Double Screw Extruder
*Screw,barrel design and manufacturing absorb European advanced technology
*Screw material:38CrMoAlA,Nitriding treated
*Adopt original famous electric components with high steady running quality.
*Omron temperature controller,ABB frequency inverter,low-voltage breaker adopts Schneider
*Gearbox adopt high torque, low noise, hard gear tooth face gear box
02 Extrusion Die
*Connection method of T-die and machine head: Flange type with bolt connection
*Die model: Cloth rack type
*Width of die layer: 1350mm
*Height of die lip open: 2mm-8 mm
03 Three-roller calender
*High quality seamless steel tube
*The roller surface with quenching treatment, then chrome plated and polished
*The hardness of base material >HRC50
*The inner structure of roller : reinforced type
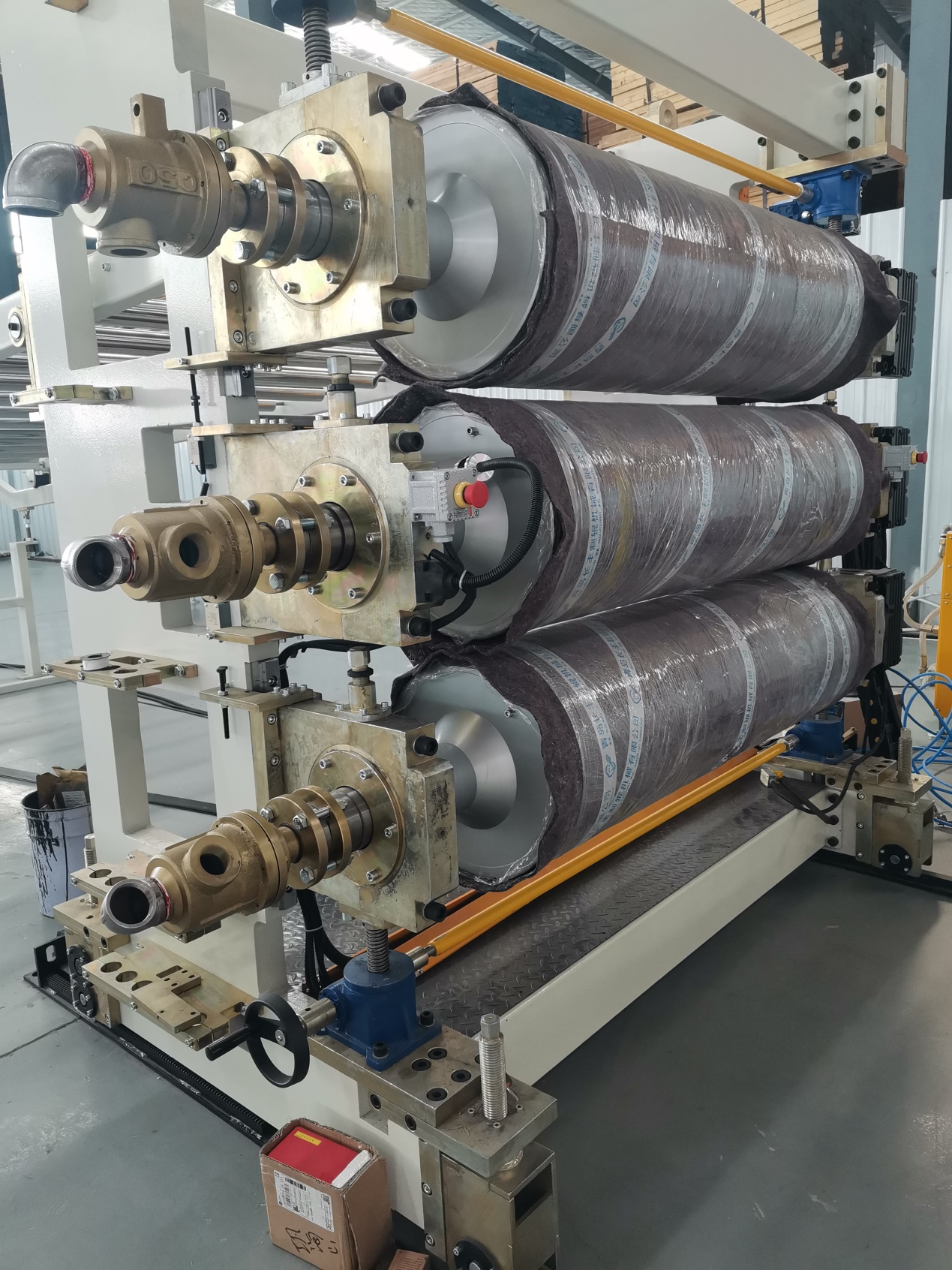
04 Oil temperature quadruple controlling system
*Model :Stand alone type
*Heat-conducting medium :High temperature heat conducting oil
*Cooling medium :Soft water
*Temperature control accuracy :±1 degree
*Heating unit :1,Stainless steel electric heating rod
*Heating power:16KW*3=48KW
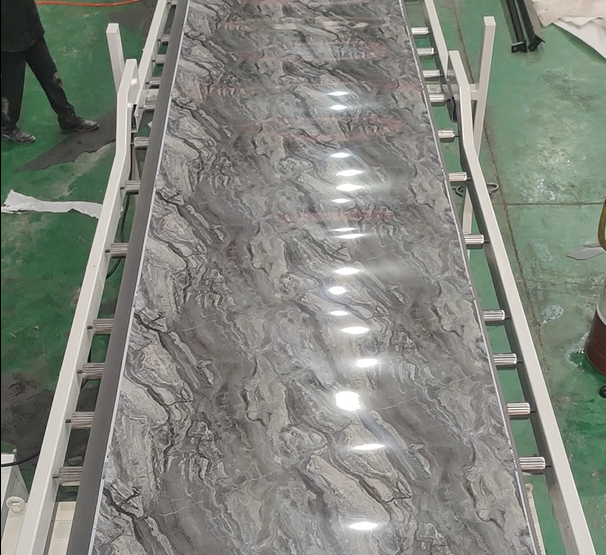
05 Cooling roller bed bracket
*Multi-group cooling rollers;
*Speed control by frequency inverter
*Compacting driving by pneumatic
*With adopts wear-resisting rubber roller
06 Rubber roller tractor
*Traction method : Active friction traction
*Roller size : Φ237mm*1500mm
*Material of roller : Rubber
*Clamping method : Pneumatic clamping
*Driving method Motor :2KW
*Traction speed : 0.4m-3.5m/min.
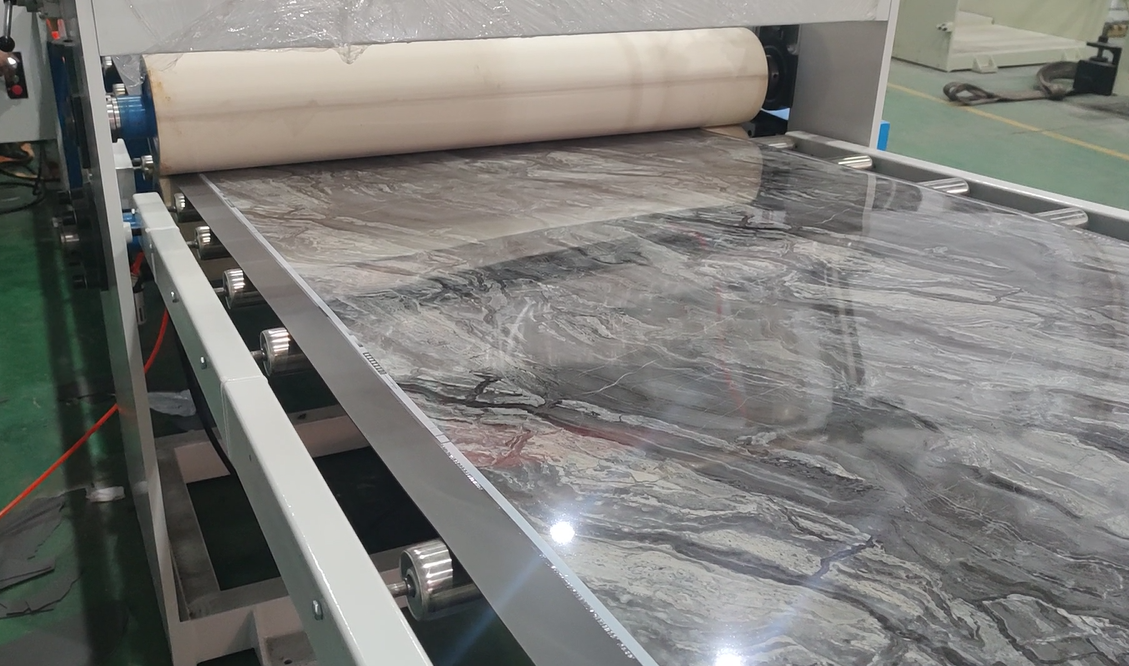
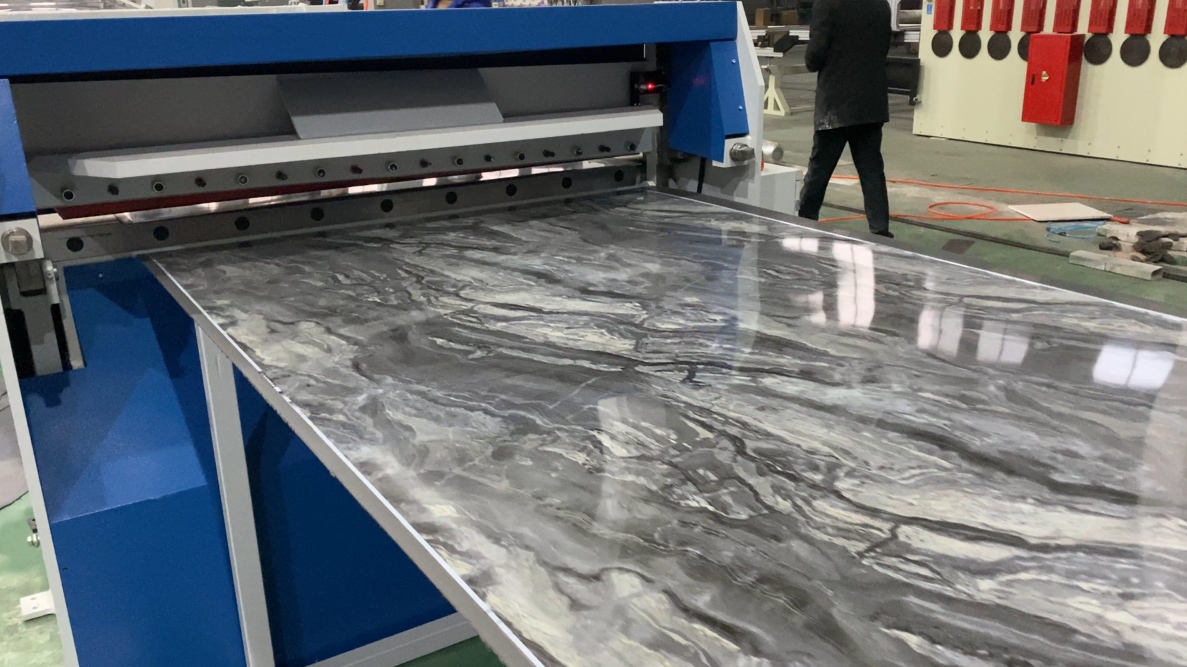
07 Cutting machine ( including bracket)
*Max cutting width : 1500mm
*Max. Cutting length : 2500mm
*Cutting thickness range : 2mm -8mm
*Motor power : 4KW
*Fixed length switch : Photoelectric sensor
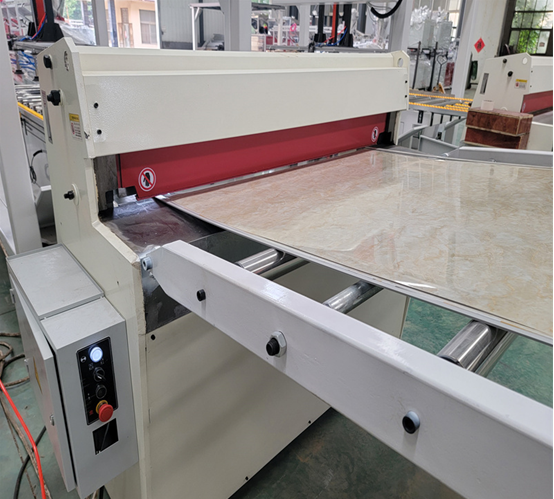
Processing Flow:
500/1000 Mixer→Auto loader→SJSZ80/156 conical twin screw extruder →Mould→ Three calender(online laminating) →Edge cutter→Hual off machine→ Transversal cutter → Conveyor→UV treatment →Final PVC marble sheet