First, the use
Our factory absorbs advanced technology to develop a series of mills for low to medium hardness plastics, especially for the processing of milling column thermoplastic PVC/PE plastic recycling grinding. The practice of the plastic products professional factory proves that the grinding powder is processed 20%-30% in the father-in-law return visit, and the chemical and physical properties of the products remain unchanged. Therefore, it is the best equipment for plastic products factories to reduce costs and reduce costs to solve the accumulation of waste products.
Second, the name model and working principle
The machine is a new type of plastic mill, its structural properties using WDJ, SMP and ACM three kinds of milling characteristics, so named WSM type. Its appearance is similar to WDJ, the door cover can be opened, easy to inspect and service maintenance, there is a screen. The feng shui double cooling using SMP can directly cool the material, blade and tooth plate, and the machine is cooled by strong wind to significantly reduce the temperature in the machine, which is conducive to the grinding of heat-sensitive clinker. In the high-speed rotating air flow of the cutterhead, the material is thrown to the tooth plate due to the action of the centrifuge, and the friction between the blade and the tooth plate is crushed. The subdivided particles are discharged with the air flow, and the coarse particles close to the tooth plate are continued to be crushed until they are fine particles due to the obstruction of the baffle and are discharged with the wind, which is similar to the internal grading device of the ACM mill。
Whether the feeding can be uniformly continuous is an important aspect that affects the efficacy of the mill, due to the different shapes of the material, the particle size is different, so the machine adopts the extractive feeding device, which adjusts the feed volume by the inlet, and the damper cover adjusts the air intake to control the speed, avoiding the problem that the feeding amount is difficult to control in the mechanical feeding device.
The low temperature is the main advantage of the machine
1、 According to the heat work equivalent: after doing work per hour into 860 kcal heat, this machine is external exhaust, the air volume is large, by the import and export of the wind temperature difference on behalf of most of the heat, a small part of the heat is solved by water cooling. Requirements: The inlet temperature of the cooling water is not more than 25, the outlet water temperature is not more than 50, and the cooling water flow is appropriately increased in summer to reduce the temperature。
2、 Third, the main technical parameters
3、 Number of cutterheads: 1 piece, outer diameter 600mm
4、 tooth plate: 1 pay (high-quality steel carburizing quenching, hardness hr60)
5、 Blade: 30 pieces (high-quality steel carburizing and quenching, hardness hr60)
6、 Spindle speed; 3000r/min
7、 Motor power: 55kw
8、 Induced draft fan model: YI32S1 power: 7.5kw
9、 Shutdown fan power: 0.75kw
10、 vibrating screen motor power: 0.25kw
11、 Output: pvc20-80 mesh output 150-360kg/h
12、 Weight: 1200kg
4. Safety precautions
Familiar with the contents of this manual and the role of each electrical button, the direction of rotation of the main unit must conform to the direction of the arrow on the belt housing.
2. Before starting the machine, the fan should be started (pay attention to steering), and after the operation is normal, the starting host reaches the normal speed and begins to add materials.
3, the beginning of production, the feeding port valve to open to small, as long as the material can come out, and then slowly open the inverter, so that the material into the machine, the load of the machine is generally about 90% of the main motor current.
4. The material selection requirements, the maximum diameter of the granules shall not exceed 15mm, and avoid the mistake of metal, stones, etc. into the machine, so as not to aggravate the wear and damage to the blade and tooth plate.
5. If there is an abnormal sound response during operation, the shutdown will be stopped immediately, and the door cover will be opened for inspection and troubleshooting before production can continue.
5. Maintenance
1. Every week, you need to open the door cover, check the blade tightening nut, and whether the cover nut is loose, if necessary.
2, lubrication: bearing grease, the first replacement cycle is used for 100 hours, the second time is 1000 hours, and then every 1000 hours
3. The fan and the pipe check its pieces and the inner wall of the pipe every month to remove the dust of its compaction.
4. After the blade has been used for a considerable period of time, when the force surface is ground into a large rounded angle, the blade splint can be removed to turn the blade 180, which can be used after tightening.
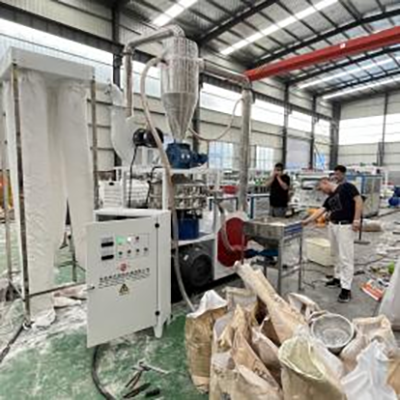
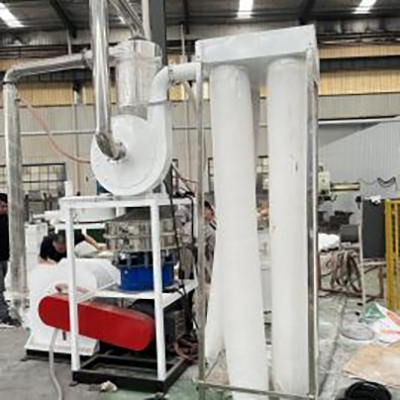
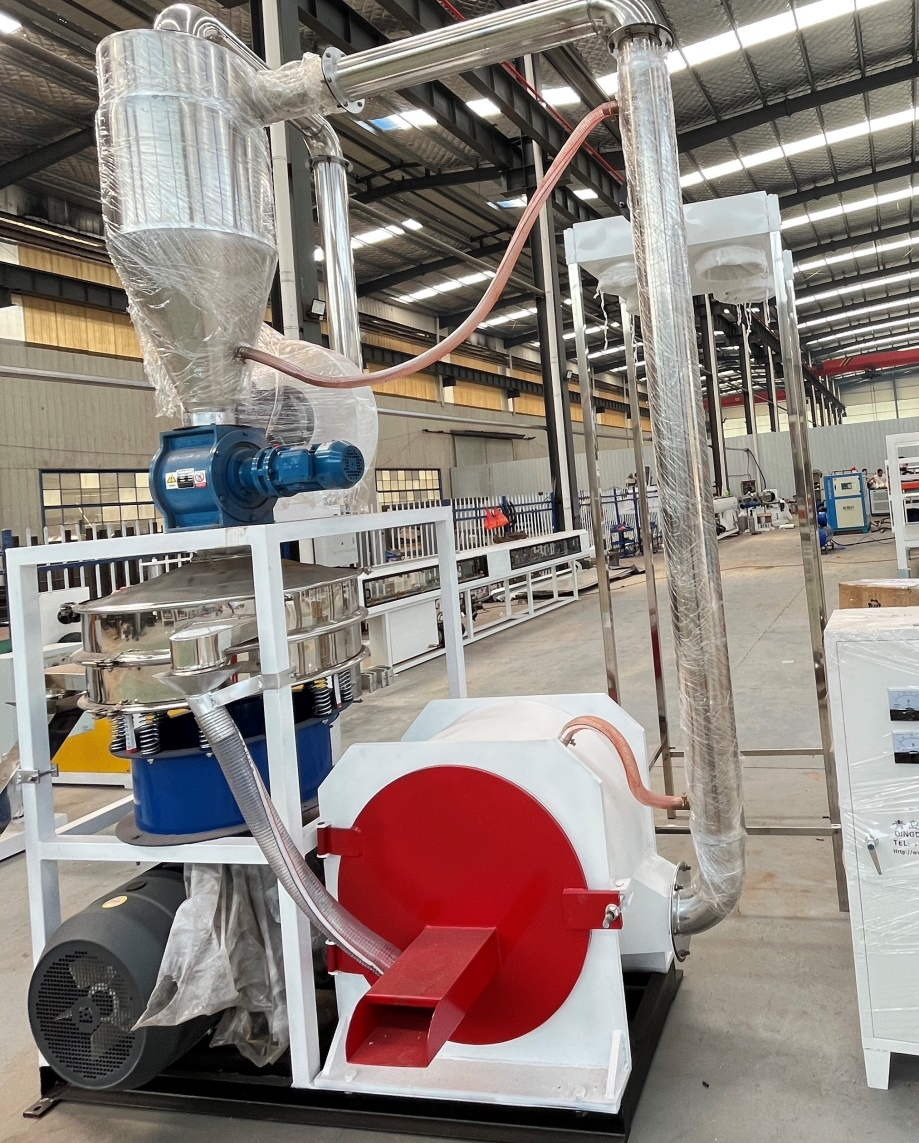
Post time: Oct-19-2023